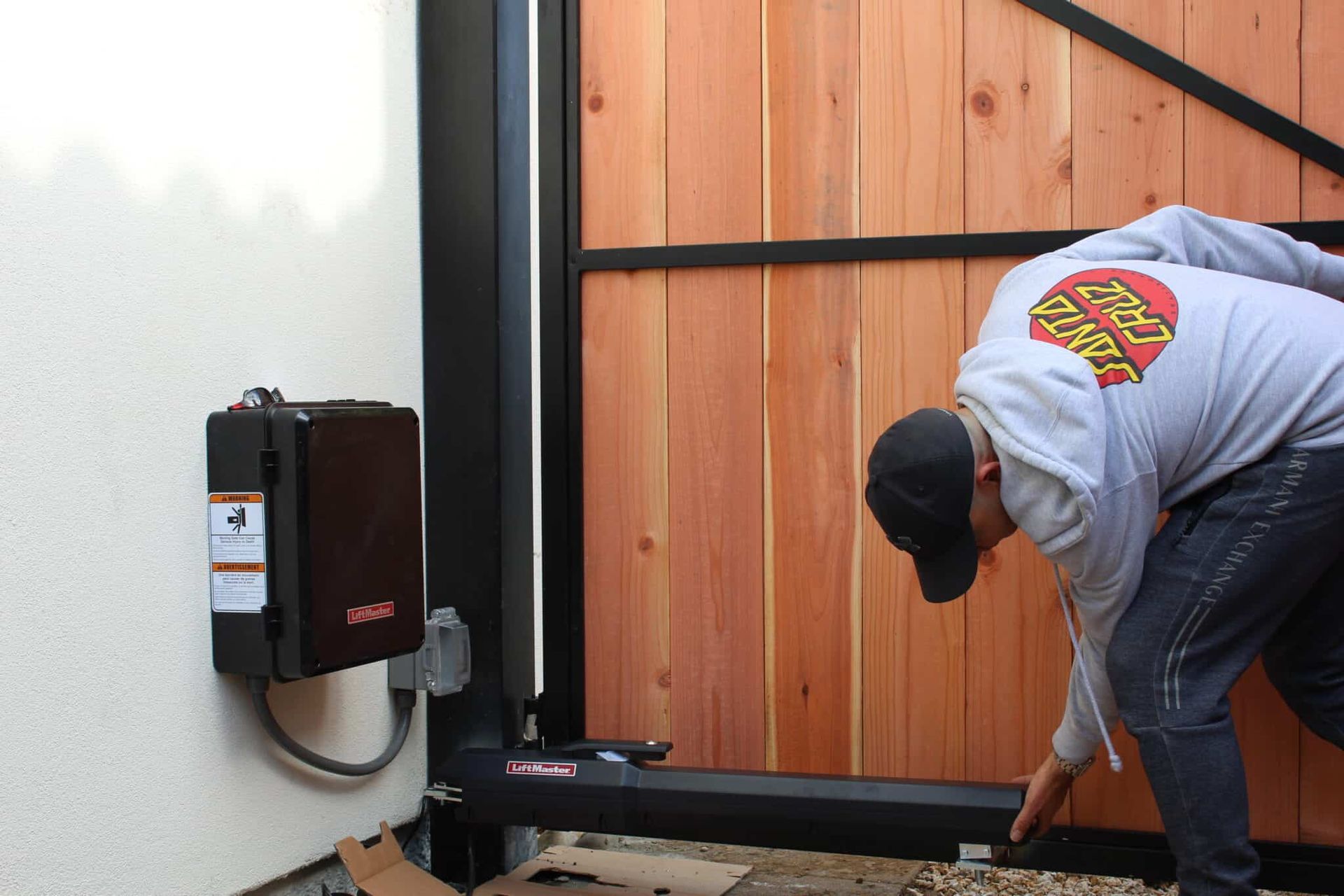
San Jose, California's #1
Liftmaster Gate Repair Service
Our experienced technicians can diagnose and repair any LiftMaster gate issue the same day you call us. We understand how important a working gate is for your security and convenience. Gates sometimes stop working when you least expect it.
Whether your LiftMaster gate won't open, close, or is making strange noises, our team has the skills to get it working again. We service swing gates, sliding gates, and all types of automated gate systems in the Orlando area.
We take pride in offering professional, expert service at reasonable prices. Our repair services start at just $39, making us one of the most affordable options around. We're licensed and insured for your peace of mind. Don't let a broken gate compromise your property's security -
call us today and we'll get your LiftMaster gate back in perfect working order.
Why Choose Us
Expertise and Experience
Our technicians undergo training to stay current with the latest gate technology developments. This expertise allows us to diagnose problems quickly and accurately, saving you time and frustration.
Quality of Service Commitment
We believe in providing transparent, honest service from the moment you call us. Our technicians arrive on time in clearly marked vehicles with all the necessary equipment to complete most repairs in a single visit.
Customer Satisfaction Guarantee
We maintain clear communication throughout the repair process. Before starting any work, we provide detailed estimates with no hidden fees or surprises. You'll know exactly what needs to be fixed and why.
Our Liftmaster Gate Repair Process
Our trained technicians follow a thorough process to ensure your gate returns to perfect working order quickly and efficiently.
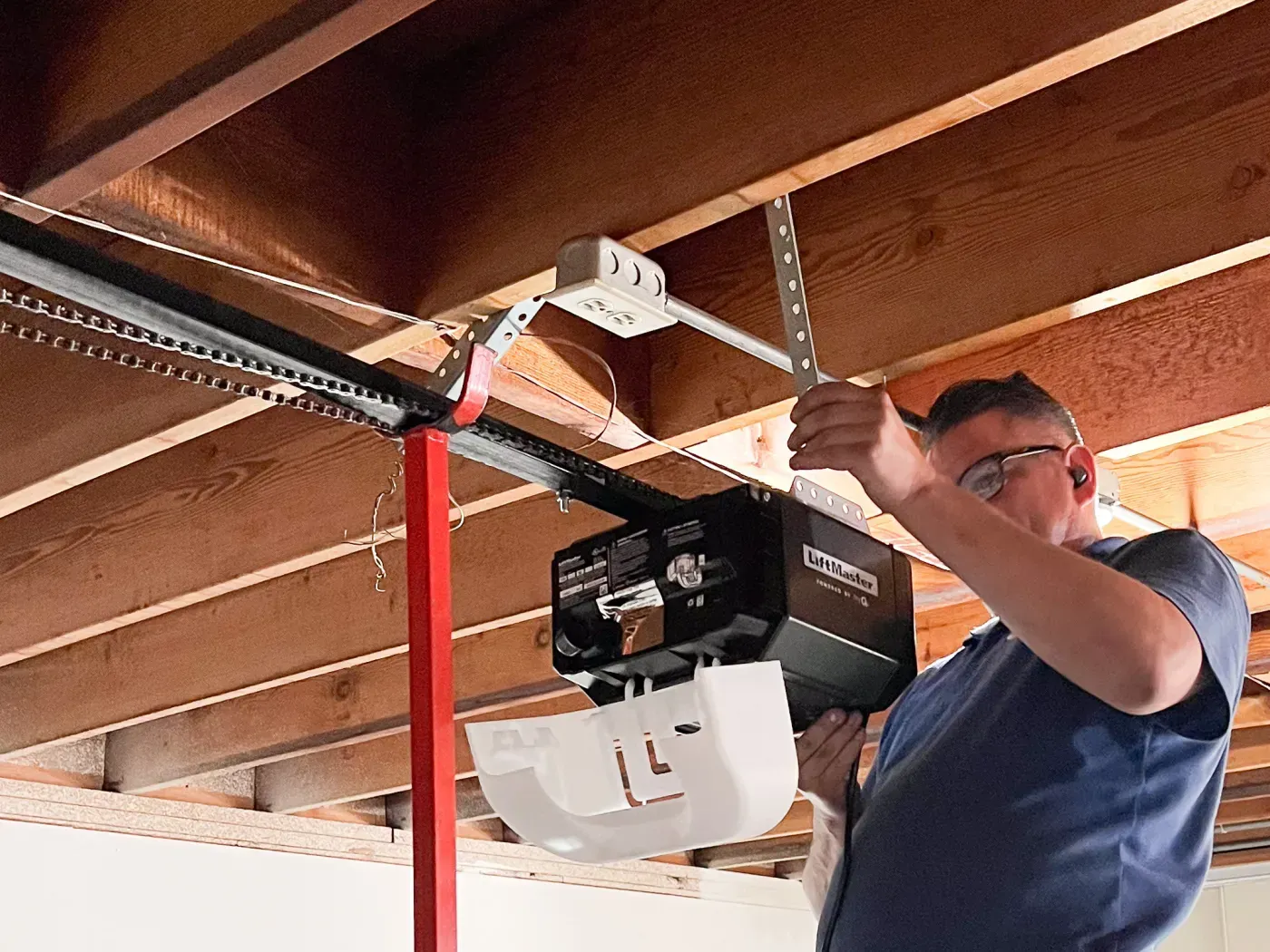
1. Initial Consultation and Diagnosis
We begin every repair job with a detailed assessment of your Liftmaster gate system. Our technicians arrive promptly at your location and carefully inspect all components including the motor, control board, safety sensors, and remote systems.
During this phase, we use specialized diagnostic tools to identify the exact cause of malfunction. Common issues we encounter include motor burnout, circuit board failures, misaligned sensors, or damaged remote controls.
We'll explain our findings in simple terms so you understand exactly what's happening with your gate. Our transparent approach means you'll receive a detailed quote before any work begins - no hidden fees or surprises later.
2. Repairing or Replacing Components
Once we've identified the problem, our technicians get to work repairing or replacing the necessary Liftmaster components. We carry common replacement parts in our service vehicles, allowing us to complete most repairs in a single visit.
For motor issues, we might need to replace worn gears or the entire motor unit. Control board problems typically require component-level repairs or full board replacement. We also fix or replace damaged sensors, remotes, keypads, and safety devices.
We only use genuine Liftmaster parts or high-quality alternatives that meet manufacturer specifications. This ensures your gate system maintains reliability and optimal performance after repairs.
3. Testing and Quality Assurance
After completing repairs, we conduct thorough testing of your Liftmaster gate system. Every repair job includes multiple open-close cycles to verify smooth operation and proper timing.
We check safety features like auto-reverse mechanisms and photo eye sensors to ensure they work correctly. Our technicians also test all access methods including remotes, keypads, and smartphone controls if applicable.
Before we leave, we'll demonstrate the repaired system and provide basic maintenance tips to help prevent future issues. We stand behind our work with a satisfaction guarantee and offer follow-up support if you have any questions after our visit.
4. Regular Inspection Schedule
We recommend inspecting your Liftmaster gate at least once every three months. Start by checking all mounting hardware and tightening any loose bolts or screws. This prevents components from shifting and causing misalignment issues.
Examine the chain or belt drive for proper tension. A sagging chain can cause jerky movements or premature wear on the motor. For LA500 models specifically, inspect the trolley nut which often needs maintenance—the K75-39337 repair kit can be useful here. Test all safety features monthly:
- Photo eye sensors should stop the gate when obstructed
- Auto-reverse mechanisms must function properly
- Emergency release should disengage smoothly
Check the battery backup system twice yearly, especially before winter and summer seasons when extreme temperatures can affect performance. Replace batteries every 1-2 years depending on usage patterns.
5. Lubrication and Cleaning Guidelines
Proper lubrication is crucial for smooth gate operation. We suggest using a silicone-based lubricant on all moving parts every 6 months. Avoid using WD-40 as it attracts dirt and can actually cause more harm than good in the long run.
Keep the gate structure clean by removing debris from tracks and moving parts. Leaves, twigs, and other environmental elements can interfere with normal operation. For coastal installations, rinse the exterior components quarterly to remove salt deposits that accelerate corrosion.
Clean the photo eye sensors with a soft, dry cloth monthly. Dirt buildup can cause false triggers or prevent proper functioning of this critical safety feature.
6. Prompt Repair and Replacement
When you notice unusual noises, jerky movements, or slow operation, don't delay repairs. Small issues often escalate into major problems when ignored. We can diagnose and repair motherboard issues, which are common in older Liftmaster models.
Pay attention to these warning signs requiring immediate attention:
- Gate stopping midway during operation
- Unusual grinding or scraping sounds
- Delayed response to remote controls
- Intermittent operation
The circuit breaker and transformer should be checked if your gate stops working suddenly. Sometimes a simple reset solves the problem. For persistent issues, inspect the fuses and replace as needed.
Battery replacement is necessary every 2-3 years for optimal performance. Watch for slower operation or reduced backup time, which indicate a weakening battery. Installing a battery heater in cold climates can extend battery life significantly.
Common Repairs for Liftmaster
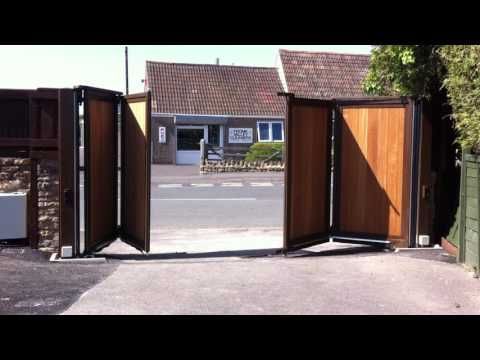
Gate Motor Issues
We often see Liftmaster gate motors that stop working properly after years of reliable service. The motor may make grinding noises or fail to open the gate completely. Sometimes, the motor struggles to start or moves too slowly. You might notice your gate taking longer than usual to respond to commands. We can quickly diagnose motor problems and either repair or replace components as needed.
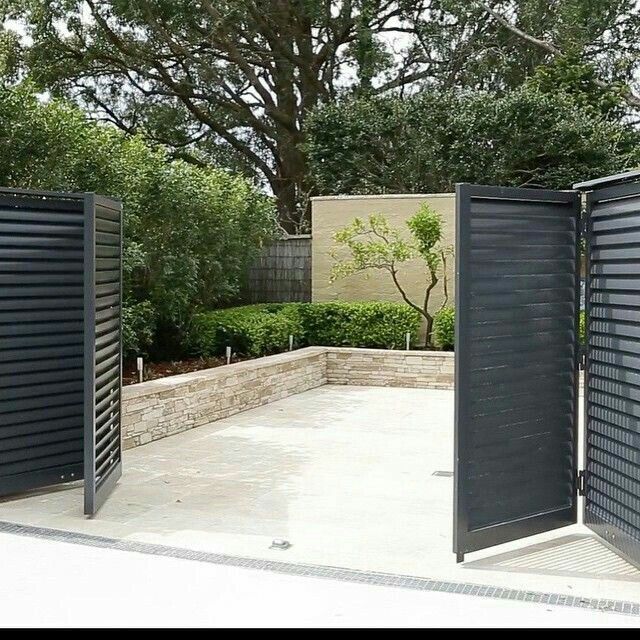
Remote Control Problems
Remote control failures are among the most common issues our customers face. You might press the button and notice nothing happens, or the gate responds inconsistently. Battery issues are often the culprit, but sometimes the remote needs reprogramming. Signal interference from nearby devices can also cause problems. We can test your remotes, replace batteries, or provide new units if needed.
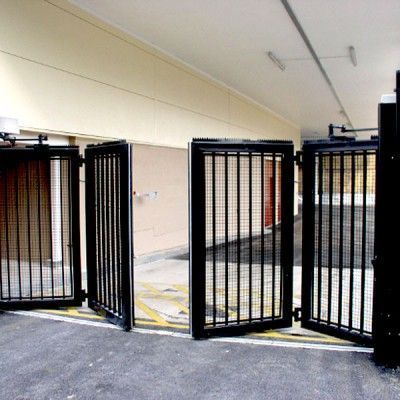
Sensor Alignment
Safety sensors are critical components that prevent your gate from closing when obstructed. When misaligned, these sensors can cause your gate to reverse unexpectedly or refuse to close. You might notice the status light blinking on your control panel. Damage from landscaping equipment or weather can knock sensors out of position. We carefully realign sensors to ensure your gate operates safely.
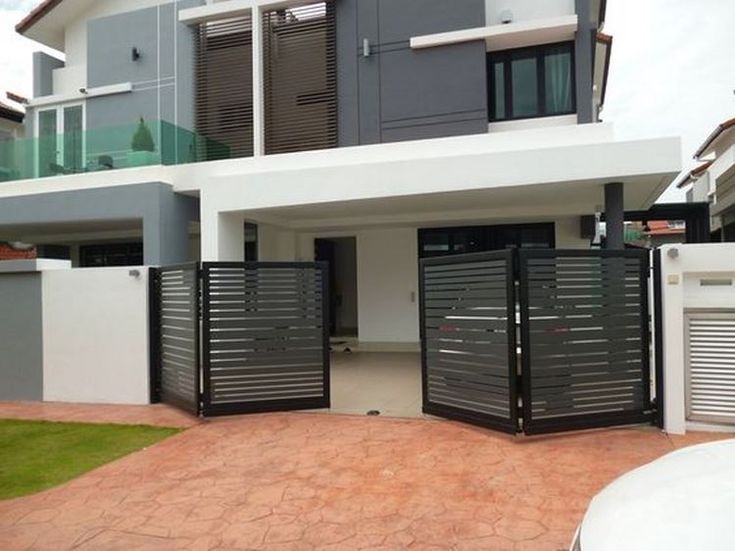
Circuit Board Failures
The circuit board is the brain of your Liftmaster system. Power surges, water damage, or simple wear and tear can cause circuit board malfunctions. You might notice erratic gate behavior or complete system failure. Sometimes, specific functions stop working while others continue. We stock replacement boards for most Liftmaster models and can install them quickly to get your gate working again.
Frequently Asked Questions
What are the typical costs associated with repairing a LiftMaster automatic gate?
Repair costs for LiftMaster gates typically range from $150-$500 depending on the issue. Simple problems like sensor adjustments or remote programming might cost less, while major motor repairs or control board replacements fall on the higher end.
We provide detailed quotes before beginning any work. Our transparent pricing ensures you know exactly what you're paying for, with no hidden fees or surprises.
How often should I service my electric gate to ensure proper functionality?
We recommend professional maintenance every 6-12 months for residential gates and every 3-4 months for commercial systems with heavy use. Regular service helps prevent major breakdowns and extends the life of your gate system.
Seasonal changes can affect gate performance, making spring and fall ideal times for maintenance visits. Gates in coastal areas may need more frequent service due to salt exposure.
What is the average lifespan of a LiftMaster gate opener?
Most LiftMaster gate openers last 10-15 years with proper maintenance. Higher-end models with quality installation can sometimes reach 20 years of reliable service.
Regular maintenance significantly impacts longevity. We've seen well-maintained systems outlast their expected lifespan by several years, proving the value of routine care.
What are common issues that require repair for LiftMaster automatic gate systems?
Remote control malfunctions are among the most frequent issues we address. These often involve signal problems or battery replacements.
Gate misalignment can occur after storms or impact damage, causing the gate to bind or stop mid-cycle. Circuit board failures may happen due to power surges or water damage.
Safety sensor issues are also common, especially after landscaping changes. According to our call data, error code 61 (safety eye interruption) is a frequent concern for many customers.
Can Xpress Automatic Gate Repair service all models of LiftMaster gates?
Yes, we service all residential and commercial LiftMaster gate models. Our technicians are factory-trained on the entire product line, from older models to the newest smart-enabled systems.
We maintain a comprehensive inventory of LiftMaster parts, allowing us to complete most repairs in a single visit. Our expertise extends to swing gates, sliding gates, and barrier arm operators.
What is included in a standard gate maintenance service by Xpress Automatic Gate Repair?
Our standard maintenance service includes safety sensor inspection and alignment, chain or belt tension adjustment, and lubrication of all moving parts. We also check motor performance and clean track systems to ensure smooth operation.
We test all safety features and ensure they meet current code requirements. Control board connections are inspected and tightened to prevent electrical issues.
Battery backup systems are tested during every maintenance visit. Our technicians also check remote control functionality and reprogram devices if needed.